|
Untitled Page
ARCHIVED FORUM -- April 2007 to March 2012 READ ONLY FORUM
This is the first Archived Forum which was active between 17th April 2007 and
1st March February 2012
Latest post 07-19-2010 12:54 PM by auric. 62 replies.
-
-
tournedos


- Joined on 12-08-2007
- Finland
- Posts 5,808

|
Re: Beogram 6000 disaster
I'll trust Tim on this
I took a look at the schematic. The solenoid feed comes from the unregulated side of the power supply, so the PS should have no damage. The solenoid driver (0TR4) is a TIP41A which is probably tough enough to blow the fuse before itself, so it is probably fine as well (check for short circuits though). If not, at least the beefier replacement TIP41C is still readily available and costs pennies.
|
|
-
-
yachadm



- Joined on 06-24-2007
- Jerusalem, Israel
- Posts 687

|
Re: Beogram 6000 disaster
Mine measures 8.89 ohms, but resistance is never the correct method to check for shorts in a winding like this. If there was a short, then the resistance should be less.
EDIT Graham reports 2ohms (but he could also be using a less precise ohmmeter...), so it MAY however be an indication of a short.
A correct method to check for shorts is Inductance, which on mine measures 5.1mH.
I've rewound these, and it's not a big deal - just patience!
A BD911 is an even sturdier replacement for the TIP41, if needed.
Menahem
Learn from the mistakes of others - you'll not live long enough to make them all yourself!
|
|
-
-
joeyboygolf
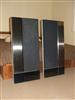


- Joined on 04-16-2007
- Ely, Cambridgeshire, UK
- Posts 3,252

|
Re: Beogram 6000 disaster
yachadm:
Mine measures 8.89 ohms, but resistance is never the correct method to check for shorts in a winding like this. If there was a short, then the resistance should be less. Graham reports 11ohms, so it just proves that resistance is not the correct tool for diagnosis (but he could also be using a less precise ohmmeter...)
Menahem
Mine measures 2 ohms Menahem, not 11. If yours measures very nearly 9 ohms then I suspect mine has a problem!!
|
|
-
-
-
yachadm



- Joined on 06-24-2007
- Jerusalem, Israel
- Posts 687

|
Re: Beogram 6000 disaster
If you've got anything in your mouth which can be measured on an ohmmeter, keep the electrics away!
Learn from the mistakes of others - you'll not live long enough to make them all yourself!
|
|
-
-
joeyboygolf
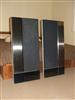


- Joined on 04-16-2007
- Ely, Cambridgeshire, UK
- Posts 3,252

|
Re: Beogram 6000 disaster
Just finished unpicking the solenoid coil which was indeed well melted. The heat had even melted the thermo plastic former.
Took me an hour to remove the copper wire which had fused in the centre of the coil and for the total thickness.
|
|
-
-
-
yachadm



- Joined on 06-24-2007
- Jerusalem, Israel
- Posts 687

|
Re: Beogram 6000 disaster
Very good!
See if you can smooth the deformity out of the plastic former, so it's a straight cylinder again.
You realise that you need magnet wire, which is insulated, and then you have to strip the insulation (usually with a hot soldering iron).
You can go up to the next thickest guage (26), with no problem.
28 guage is 0.32mm with 65 ohms/1000ft
27 guage is 0.36mm with 51 ohms/1000ft
26 guage is 0.40mm with 41 ohms/1000ft
25 guage is 0.45mm with 32 ohms/1000ft
Assuming that we all have 27 guage on all our identical coils ;-), and my resistance shows at 8.9 ohms, then the length of the copper wire should be 8.9 / 51 x 1000ft = 175 ft.
Graham can you confirm that - then we'll know you're on the right track.
If that's correct, then what you really want after that, is a winding which achieves inductance of 5.1mH (milliHenry). You can achieve that with any of the above wires, but the thicker the wire, of course, you're going to have a thicker coil. I'm not sure how much.you can exceed the dimensions of the former though.
The upside of using a thicker wire is that the coil will always run cooler.
Let us know what your copper wire length is, and after that if you can get 27 or 26 guage wire.
Menahem
Learn from the mistakes of others - you'll not live long enough to make them all yourself!
|
|
-
-
Stonk
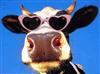

- Joined on 04-16-2007
- Marlow, Bucks, UK
- Posts 1,688

|
Re: Beogram 6000 disaster
Graham, is this the Beogram that slid off the back car seat when your son collected it for you? If so you can blame him for the damage and get him to rewind the coil as compensation
If you think nobody cares, try missing a couple of payments.
|
|
-
-
joeyboygolf
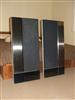


- Joined on 04-16-2007
- Ely, Cambridgeshire, UK
- Posts 3,252

|
Re: Beogram 6000 disaster
Stonk:
Graham, is this the Beogram that slid off the back car seat when your son collected it for you? If so you can blame him for the damage and get him to rewind the coil as compensation
Yes, it's the very one. Thanks to the kindness of Peter and Lee I have fitted what looks like a brand new wooden surround, fitted a NOS MMC20CL, treated it to a lube and new belts and it is my pride and joy. Until......the smoke[:'(]
|
|
-
-
-
tournedos


- Joined on 12-08-2007
- Finland
- Posts 5,808

|
Re: Beogram 6000 disaster
I would probably keep the jig manual - there aren't that many turns in the winding, and once you get bored and really get the motor going you'll mess up sooner or later, have to back up and the wire gets kinked.
Should work with a hand crank on the solenoid side and somebody (you apparently already have a volunteer ) braking the wire reel to keep the wire taut. Keep the solenoid and reel a meter or so apart so the wire stays near to perpendicular to the solenoid. Wear gloves!
But if you have a drill that can be easily driven slowly it should work as well. Saves building the axle and crank for the solenoid side.
|
|
-
-
joeyboygolf
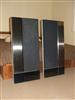


- Joined on 04-16-2007
- Ely, Cambridgeshire, UK
- Posts 3,252

|
Re: Beogram 6000 disaster
I have tried rewinding with the 27 AWG wire and end up with a coil with 7.4 ohms resistance when packed level with the top of the sides of the former.
I re-fitted this to the deck and as I suspected, it does not have the strength to operate the mechanism fully. I will rewind, trying to pack the absolute maximum amount of wire on the former. Can I wind anther 1.5 ohms worth? I doubt it. (Another 30+ feet!)
As a back up, I have ordered 28 AWG wire which should enable me to get more turns on the former and hopefully increase the power of the solenoid. Anyone care to comment 'cos I am working somewhat in the dark here!
|
|
-
-
nobby


- Joined on 04-21-2007
- Posts 539

|
Re: Beogram 6000 disaster
You are doing fine 
This is how you learn!
|
|
-
-
tournedos


- Joined on 12-08-2007
- Finland
- Posts 5,808

|
Re: Beogram 6000 disaster
joeyboygolf:
As a back up, I have ordered 28 AWG wire which should enable me to get more turns on the former and hopefully increase the power of the solenoid. Anyone care to comment 'cos I am working somewhat in the dark here!
I've never rewound these solenoids, but... generally if the dimensions of the coil and the current through it remain the same, the magnetic field is directly related to the number of turns in the winding. So you should aim to keep the DC resistance at the 8-9 ohm range while maximizing the number of turns.
If it almost works now, I suppose the next thinner wire will be fine as you should be able to squeeze in more turns even if the length of the wire might be shorter (for 8-9 ohms).
|
|
-
-
joeyboygolf
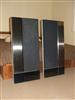


- Joined on 04-16-2007
- Ely, Cambridgeshire, UK
- Posts 3,252

|
Re: Beogram 6000 disaster
I'll try a rewind with the 27 AWG wire and see if I can get another 30+ feet of wire on the former.
If that fails then I'll have to wait until the 28 stuff arrives, probably not until Tuesday.
I've plenty of other decks to use in the meantime but somehow they are not the same.
|
|
-
-
joeyboygolf
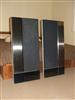


- Joined on 04-16-2007
- Ely, Cambridgeshire, UK
- Posts 3,252

|
Re: Beogram 6000 disaster
I rewound the solenoid this morning packing as much wire as possible onto the former. To my surprise, the resistance of the coil measured at 10 ohms!
Reassembled this afternoon and.........it works!
There is an intermittent problem with the arm lifting in the middle of a record and dropping straight away to continue playing but I had this problem before on occasions.
I will continue with efforts to obtain an undamaged solenoid as the former on mine is damaged beyond repair. However, it does at least work for now.
Picture attached of the rewound solenoid and the plastic pad which now triggers the microswitch to reduce the voltage once the system has activated. Holding voltage is 3 volts.
So, anyone have a solenoid from a Beogram 4000, 4002 or 6000 Quad or a microswitch that still has the plastic tit on that they are willing to part with please send me a PM.
|
|
-
-
yachadm



- Joined on 06-24-2007
- Jerusalem, Israel
- Posts 687

|
Re: Beogram 6000 disaster
Graham
I think you've done a fantastic job. I wouldn't bother looking for an original - I think yours is better. I'll bet the inductance on yours is higher than the original, which means that the plunger works much more positively. The electrical circuit is strong enough to handle the extra resistance.
Keep yours!!!!
Menahem
Learn from the mistakes of others - you'll not live long enough to make them all yourself!
|
|
-
-
joeyboygolf
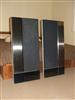


- Joined on 04-16-2007
- Ely, Cambridgeshire, UK
- Posts 3,252

|
Re: Beogram 6000 disaster
Thanks for the comment Menahem, it does seem to work with a good solid clunk!
Maybe you can help with this problem that I have never seen before. The solenoid operates and sometimes, rarely, begins to chatter??
My thought is to replace the 1N4004 diode that is across the solenoid leads. You do mention this in your article but not this particular fault?
Your comments would be appreciated.
|
|
-
-
tournedos


- Joined on 12-08-2007
- Finland
- Posts 5,808

|
Re: Beogram 6000 disaster
The only purpose of that diode is to protect the driver transistor from reverse voltage spikes from the solenoid, it shouldn't have any effect on that problem. I'd try cleaning the microswitch contacts first.
(and I agree your current solenoid is fine!)
PS. Just re-downloaded the service manual since I didn't have it on this computer. Seems like Peter has rescanned it recently, as it now includes a couple of service bulletins from 1975 - the first one tells that the switch arm has been changed from plastic (as my broken one) into metal (as yours) to prevent solenoid burn-up. Another tells that intermittent arm lifts and interruptions are caused by a noisy RPY 58 photo resistor in the arm position encoder... as seems to be your problem, and what I was fighting with when I got my BG6000 2+ years ago!
|
|
-
-
yachadm



- Joined on 06-24-2007
- Jerusalem, Israel
- Posts 687

|
Re: Beogram 6000 disaster
Yes, I'd definitely look at cleaning the contacts first.
Mika, was it you who suggested rerversing the RPY58 photo-resistor, in the absence of new ones being available?
Menahem
Learn from the mistakes of others - you'll not live long enough to make them all yourself!
|
|
-
-
tournedos


- Joined on 12-08-2007
- Finland
- Posts 5,808

|
Re: Beogram 6000 disaster
Not me. I think it was auric?
Anyway the service bulletins suggest a few fixes, including replacing the RPY 58 with a phototransistor, and others that resemble the ad-hoc RC filter additions I used to circumvent the problem. When I debugged mine, the encoder circuit really was getting spurious pulses apparently out from nowhere, so it probably was indeed pulse noise from the RPY 58 when it was supposed to only "see" black. Here's that thread if anyone wants to review it.
And the modifications (including the plastic to metal switch arm upgrade) should've been free to the owners until March 1976, but apparently all dealers weren't that active doing the recalls...
Check out these bulletins, Graham, if yours has an incandescent bulb instead of an IR LED in the position marker circuit (which means it probably used the RPY 58 originally). They are in the end of the BG4002 service manual on site, types 5514-5524.
|
|
-
-
joeyboygolf
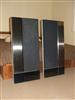


- Joined on 04-16-2007
- Ely, Cambridgeshire, UK
- Posts 3,252

|
Re: Beogram 6000 disaster
Yes, mine has an incandescent bulb , I can see the filament through the plastic housing.
I'll do the mod and see what happens and at the same time I'll get the bits to do Menahem's LED mod. Belt and braces as we say in the UK!
|
|
-
-
auric


- Joined on 04-16-2007
- Posts 357

|
Re: Beogram 6000 disaster
Hi Graham:
You can make your own former!
Go to a hobby shop and buy similar diameter acrylic rod and cut to length. You can then saw off the two end caps from the old former or find appropriate sized plastic washers. Glue on both ends of the acrylic rod and wind your coil.
You can also use a copper tube. The model aircraft people will have them. For extra ruggedness you coat the road copper tube with varnish/paint or put heat shrink tubing or craft paper over it before winding.
Derek
|
|
-
-
yachadm



- Joined on 06-24-2007
- Jerusalem, Israel
- Posts 687

|
Re: Beogram 6000 disaster
Hi Derek,
I wouldn't guarantee that the piston would move - you'd be changing the electric field-strength acting on the piston, unless the hole's diameter was EXACTLY the same as the original, and the plastic former's thickness also the same.
Menahem
Learn from the mistakes of others - you'll not live long enough to make them all yourself!
|
|
|
|
|