|
Untitled Page
ARCHIVED FORUM -- April 2007 to March 2012 READ ONLY FORUM
This is the first Archived Forum which was active between 17th April 2007 and
1st March February 2012
Latest post 05-01-2010 12:10 PM by Paul. 19 replies.
-
-
-
Dillen
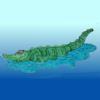

- Joined on 02-14-2007
- Copenhagen / Denmark
- Posts 5,008

|
I'm sure you will find that most signal path caps are still fine, strange as it may sound. If you will have to replace some, I would suggest mounting electrolytics again. The ones most prone to failure are the three large cans (Power supply and the speaker outputs). Note the polarity of the power supply cap, the Beomaster 1000 has positive ground !
Martin
|
|
-
-
Paul


- Joined on 12-20-2008
- USA
- Posts 108

|
Thanks Martin
The power supply cap appears to be bad and I suspect the 2 outputs also.
I have noticed this unit has more axial electrolytics than most.Some in the PS and quite a few in the MPX section.These all appear to be very bad,having obvious blow-out at the ends.Can't wait to hear this thing with some good caps in it.
Paul
|
|
-
-
chartz
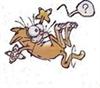


- Joined on 07-20-2009
- Burgundy
- Posts 984

|
Hi,
I can confirm what Martin says, electrolytics on the signal path are fine. I changed my BM 6000 caps with identical types (not Chinese ones though!) and the sound is perfect. Blind tests have shown little or no difference in sound quality when you install "better" caps. I tried polyprops in the phono stage but reverted to original caps, because I couldn't hear the difference, and I have a looong experience in hi-fi, believe me, having tested transistor and valve. When you spend money on expensive components your brain tells you they are better, but are they? Methinks this is a placebo effect.
Jacques
|
|
-
-
Paul


- Joined on 12-20-2008
- USA
- Posts 108

|
Thanks Jacques
It is nice to hear some voices of reason on this subject.Glad to hear it,the polyesters are a bit hard on the wallet.I have heard much about the "evils" of electrolytics in the signal path,especially tantalums.I was always a bit skeptical,considering some fine sounding B&O gear is loaded with normal electros and tantalums.I do believe in the value of a good quality cap though,for longevity,if nothing else.My main concern at the moment,is that I heard the tantalums tend not to just slowly wear out but actually explode unexpectedly.Any thruth to this?
Paul
|
|
-
-
-
Dillen
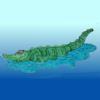

- Joined on 02-14-2007
- Copenhagen / Denmark
- Posts 5,008

|
Well, obviously, if you can see (or measure) that they are bad, you should of course replace them. Leaks and blow-outs are clear signs that they would like to be replaced. I would mount new electrolytics rather than polyesters.
The large power supply filter capacitor CAN explode and it's a terrific experience. 
Martin
|
|
-
-
-
Die_Bogener


- Joined on 04-16-2007
- Bogen, Germany
- Posts 1,010

|
I have seen several exploded tantalum caps in old computer boards and some very old Telefunken / Philips Tape machines.
Tantalum explodes like a firecracker und burns like a candle, leaving only two burnt wires on the board... but all these were used in power supplies, not in the signal path. In the signal path there is not enough power available to burn.
Tanatlum has pretty bad acustic characteristics. If you replace them by MKT/MKS types, the sound will change a lot. The old fashioned sound will get lost to a more clearer sound. It will sound more modern.
I would not change every electrolyth caps to a MKT type, it's way to expensive and in most cases not necessary. There is no sense to replace them in a power supply, only if it becomes really hot the MKT will extend lifetime.
|
|
-
-
-
classic



- Joined on 04-16-2007
- Venø - Struer / Denmark
- Posts 224

|
This is an interesting discussion.
I see the issue from another angel. A classic product can be restored in various ways:
1. Replacing the signal path caps with MKT/MKS caps
2. Replacing the signal path caps with audio grade electrolytic caps
3. Replacing selected caps only
4. Replacing the signal path caps with the original caps technology selected by Bang & Olufsen at the time of design.
1 and 2 will give a more ‘clear’ sound which for many will be an improvement. 2 will be the most ‘warm’ sound.
For me there is no doubt, I always replace all electrolytic caps in a product. I replace the caps with the original technology because I want to ‘obtain’ the original sound of the product. This means I replace tantalum caps with new tantalum caps of course.
If you are in doubt regarding to replace a few visual critical caps or all caps a measuring of the ESR of a few of the 30 years old caps will give you the reply.
Replacing all electrolytic caps also means decoupling caps and power supply caps.
/Frede
Beolab 5000 - "If another amplifier sounds different then it needs repair!"
|
|
-
-
Dillen
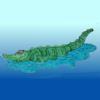

- Joined on 02-14-2007
- Copenhagen / Denmark
- Posts 5,008

|
I agree with Frede though we must also decide whether to repair, restore (or "modernize"). In a repair situation, I like to replace mainly the faulty components and maybe a few extra known troublemakers. In a restoration, I also replace the whole lot and also try to mount correct types of caps unless a certain type of cap is known to cause problems in a specific position.
If Paul is aiming at a complete restoration, I suggest he replace all the electrolytic capacitors. Most 25+ year old electrolytic capacitors will have died or at least become marginal by now anyways so in practice repairs to things of that age tend to lean against restoration.
I really like the original sound of the old Beomasters so I would definitely go for original type capacitors.
Martin
|
|
-
-
Paul


- Joined on 12-20-2008
- USA
- Posts 108

|
Wow,so many good responses.I'm glad I asked.
On my last project,a BM3000-2,I replaced every electrolytic.Everything under 10uf was replaced with Polyester caps(most of these were originally tantalums).The balance of the electrolytics were a mixed bag of audio grade electrolytics and computer/industrial grade.This 3000-2 now sounds excellent but I do see where it has become "sterilized".There is very little vintage "warmth" at all.I'm not implying that this is a bad sounding receiver at all.Quite the contrary,this more modernized sound is very detailed and precise.Many listeners will find this favorable to the old school vintage sound.
Now on my new BM1000,I wanted to do something different,hence this thread was started.I figured a small,low powered,simple amplifier like this one which is 40+ years old, would best be restored to it's original vintage tone. Summing up the wealth of info I have gotten here(hopefully more to come too) I have come to some conclusions:
- putting polyesters in for coupling will indeed take away some of the the vintage tone and create a more modern sound.(Not to mention,they are more expensive and at times hard to fit.)
-New electrolytics and tantalums are both suitable replacements and help preserve original tone characteristics.(more affordable and easy to fit)
Can someone share their experience with the use of modern audio grade electrolytics in vintage equipment versus computer grade/standard grade/industrial?Will these tend to alter and modernize my sound as well?
Paul
|
|
-
-
yachadm



- Joined on 06-24-2007
- Jerusalem, Israel
- Posts 687

|
Paul,
You're on the right track - but on the actual signal path itself, remember that the coupling caps are there primarily to block DC (the best capacitor is no capacitor at all), so the objective is have a capacitor which affect the signal audio as neutrally as possible.
Today, with the advanced technology of film caps (Wima MKS2), you can quite easily use a 2.2uF Wima cap instead of the original 50uF (or even higher value).
I've routinely used Wima 3.3uF as a substitute for an electrolytic 220uF. And the Wima does a better job of blocking the DC.
The much smaller value means even less signal coloration than the original high uF electrolytic.
And that, after all, is the end goal of audio - to ensure that the original sound reaches the ear of the listeners.
Bear in mind, I am talking about only the coupling caps on the signal path, nowhere else.
As far as tantalums go, unless they have an inbuilt fuse (check the manufacturer's data), they are simply dangerous to the "unobtanium" vintage semiconductors. When tantalum fails, it fails shorted (whoosh - poof - smoke). When all other caps fail, they fail open.
Nichicon has very affordable 105C Audio caps now - the KT series. I standardize basically on Panasonic EB for almost everything on the PCB, and KT's around the signal. A few Wima's in the signal path, and the total capacitor cost on a complete restoration is not frightening at all.
Menahem
Learn from the mistakes of others - you'll not live long enough to make them all yourself!
|
|
-
-
yachadm



- Joined on 06-24-2007
- Jerusalem, Israel
- Posts 687

|
And while we're at it, looking for the purest way to keep the original music from getting colored by the components, don't forget the resistors.
Those original carbon resistors are NOISY, notwithstanding that many of them are no longer in spec.
On restorations where money is no object, I replace every resistor. The difference is not only audible, but visible as well - watching the scope signal - it's incredibly stable. Taken at certain points in the circuit, before and after.
My favorite for absolutely zero coloration is the Vishay Dale CMF55 or CMF60 Metal film series. I'm sure that if B&O were keeping to their original mandate, they'd be using these resistors instead of the (I won't mention it) that I am shocked to see when I open up their modern stuff.
All of B&O's original suppliers are now under the Vishay banner, but B&O apparently (from looking under the hood) has abandoned those suppliers.
Stay away from Carbon and Metal Oxide types in audio work - very noisy, and therefore alter the sound unpredictably.
Wirewound ($$$$$) and Metal Film are the quietest and most neutral, and Carbon Film thereafter.
But you can certainly look at replacing the resistors in the signal path area only, as a limited-expense improvment.
Menahem
Learn from the mistakes of others - you'll not live long enough to make them all yourself!
|
|
-
-
Paul


- Joined on 12-20-2008
- USA
- Posts 108

|
Thanks Menahem
I won't be doing the full,cost no object,type restoration you mentioned but I will indeed be checking the resistors and replacing as nessessary.I have used the Dale resistors you mention in some of my tube projects.
In regards to the caps I think I will take things slowly.I will first get the power supply caps replaced and get my idle current and supply voltage to spec then I will start dropping in pairs of caps,grab a beer and pause and listen for changes to the sound.I know the sound I am after,and I detect a hint of it in there even with the bad caps.If I don't like the direction the tone is heading as I do my replacements,I will substitue something else.I find this model relatively easy to work on,making a quick change of caps easy without a total disassembly.
Paul
|
|
-
-
-
Dillen
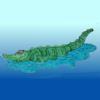

- Joined on 02-14-2007
- Copenhagen / Denmark
- Posts 5,008

|
If the goal is to achieve original sound and general functionality, I must say that I don't agree to replace all components on sight. I never do anyways but rather try to stick with originality as far as possible and let vintage be vintage.
Menahem tend to prefer replacing all components that he can find modern substitutes for in an attempt to reach a higher degree of stability or linerity or something else. He knows that I don't always agree with him, I respect his choices and paths even if I don't always understand them. He works in a different way than I and this is not to stir up a discussion but it's a fact that the original circuit was never constructed with 40+ years future components in thought and lots of the modern components would perform much better if the circuits themselves too were re-engineered. But then we would end up with a modern circuit with modern components and you can buy that in nice plastic casings in any HiFi shop today. Much cheaper and with remote control, USB 2.0, wireless network and no bigger than a pack of cigarettes. It would never be a Beomaster 1000 - but that's just my opinion.
The number of capacitors in a Beomaster 1000 is not that high so it would not be an impossible or too costly task to replace the lot. If physically broken, leaking or otherwise proven defective they must be replaced and in most cases you can apply the rule that if one cap is bad, others of similar types in the same machine will also be, so that will save you some measuring and you can do all the shopping in one go.
Personally, if the radio is performing well by then, I wouldn't worry too much about resistors, transistors, diodes etc. If the components are still working, they will have proved their reliability and there's a good chance they will continue to do just that. The old components will have fairly large tolerances on their values but the radios circuits were constructed with this in mind.
A Beomaster 1000 is a wonderful radio in its own right. I have quite a few in my own collection, more than sanity allows, and I've repaired several from all over the world. Everytime I have one on the bench I sit back and listen. I truely enjoy the wonderful sound it produces.
Yes, it may not have a completely linear frequency response. Yes, it may have a slight hint of background noise, especially if its an early (germanium) version. Yes, it's not a modern construction. But that's how it was intended.
Allow it to play using contemporary B&O speakers or slightly newer, Beovox 1000 or preferably higher, and I'm sure you'll also be amazed.
Martin
|
|
-
-
Die_Bogener


- Joined on 04-16-2007
- Bogen, Germany
- Posts 1,010

|
... and if you only change defect caps or caps in the sound path, there is no need to readjust anything. Adjusting an amplifier is pretty easy, but the radio section is a complete different thing.
I would never replace anything in a tuner that is not an eletrolyth cap. Especially ceramic caps in the tuner section are very, very difficult to replace, since the complete adjustment is changed... and usually the effect is not better than original.
|
|
-
-
Paul


- Joined on 12-20-2008
- USA
- Posts 108

|
Thanks for the great input guys!
I can clearly see the differing opinions on this topic.I expected it,and I welcome it.I am glad to hear the experts opinions and am thankful that no one is holding back simply to be agreeable.As I stated in the opening of the thread,I want to attempt to preserve the original vintage tone of this machine.This may be easier said then done for a few reasons:
-I have to put in new caps.Most the caps(electros)look horrible.I simply don't trust them at 40+ years old.I suspect the new caps that I have available,no matter what I choose,will have different characteristics than original.
-I am replacing all the tantalums,but I am not planning to install new tantalums.I understand Frede installs new tantalums in his professional quality Beolab Restorations,where he leaves no stone unturned to preserve the original sound,and of course his record speaks for itself.But in my case,I have a large stock of many types of electrolytics and polyesters,so this is what I will be using.From what I have learned in this thread,This alone is likely to change the sound.
-I have no idea what this thing sounded like to begin with anyway,I was a baby when it was new!
My theory is that I can,by proceeding slowly,changing cap by cap(or pairs),and listening carefully,preserve the original tone within reason.Also modern components(metal film resistors,closer tolerances,audio grade caps,polyester caps)used appropriately,will be able to make improvements in performance as well without taking away the original tone.Just a theory,of course,but I am not happy unless I'm at the workbench anyway.
Thanks again to all for all the excellent input
|
|
Page 1 of 1 (20 items)
|
|
|